This past Friday CIADC and Embarc Chicago joined forces to bring local students from Sullivan High School into the shops for a day of immersive education, access and community. The kids jumped right in and knocked out projects from three of our departments: Metalworking & Forging, Woodworking, and Casting & Molding.
In each department, the student’s eyes were wide but focused as they worked. In the Metal Shop, Olivia taught the students how to forge, hammer and twist a piece of bar stock into a handy key fob. Up in the Woodshop, Erik guided the students on the bandsaw to produce a small box. And in Casting & Molding, Micki and Julia had the students independently design their own scratch molds and then poured 1,200 degree hot aluminum get poured into them to create a cast of their design.
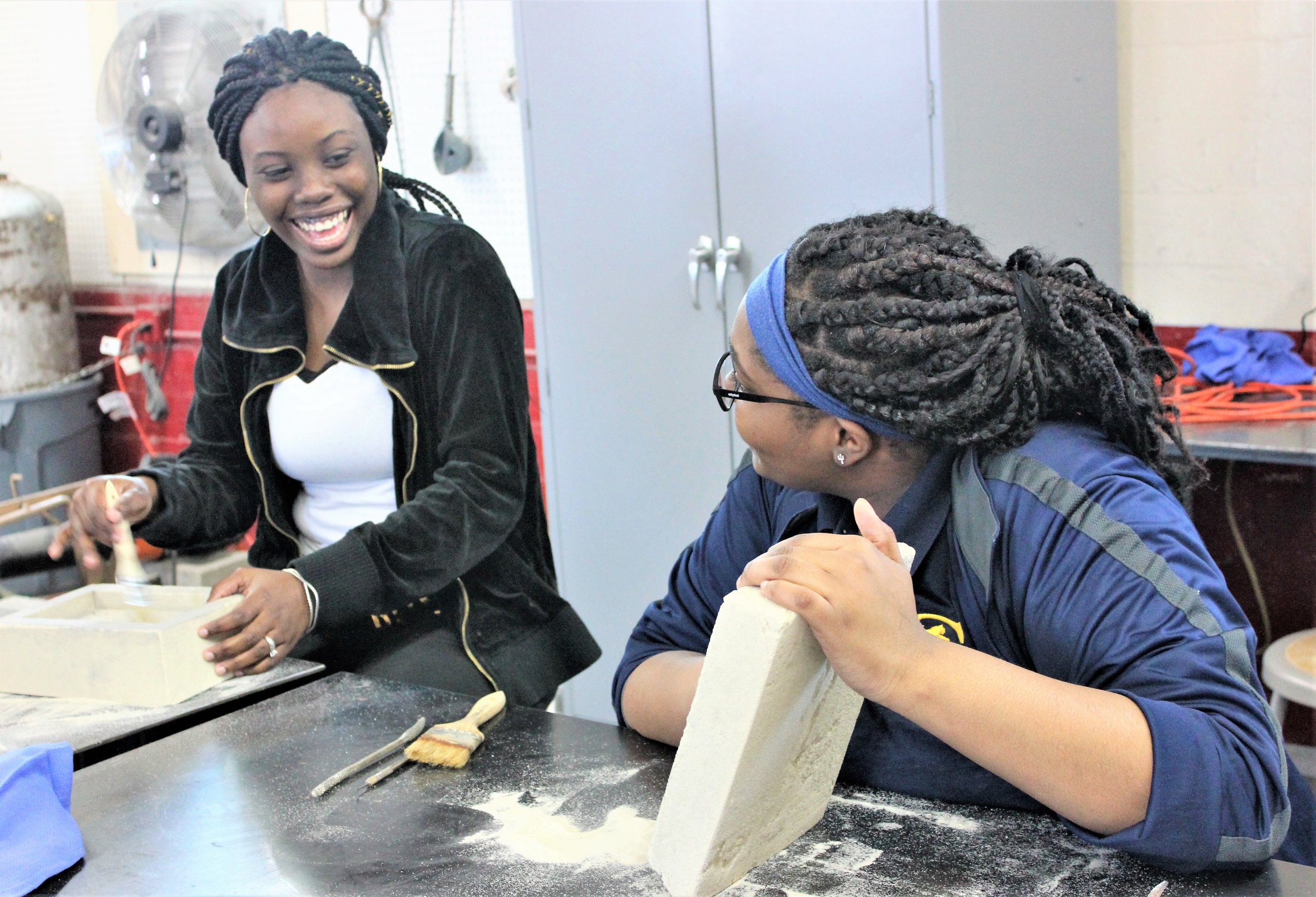
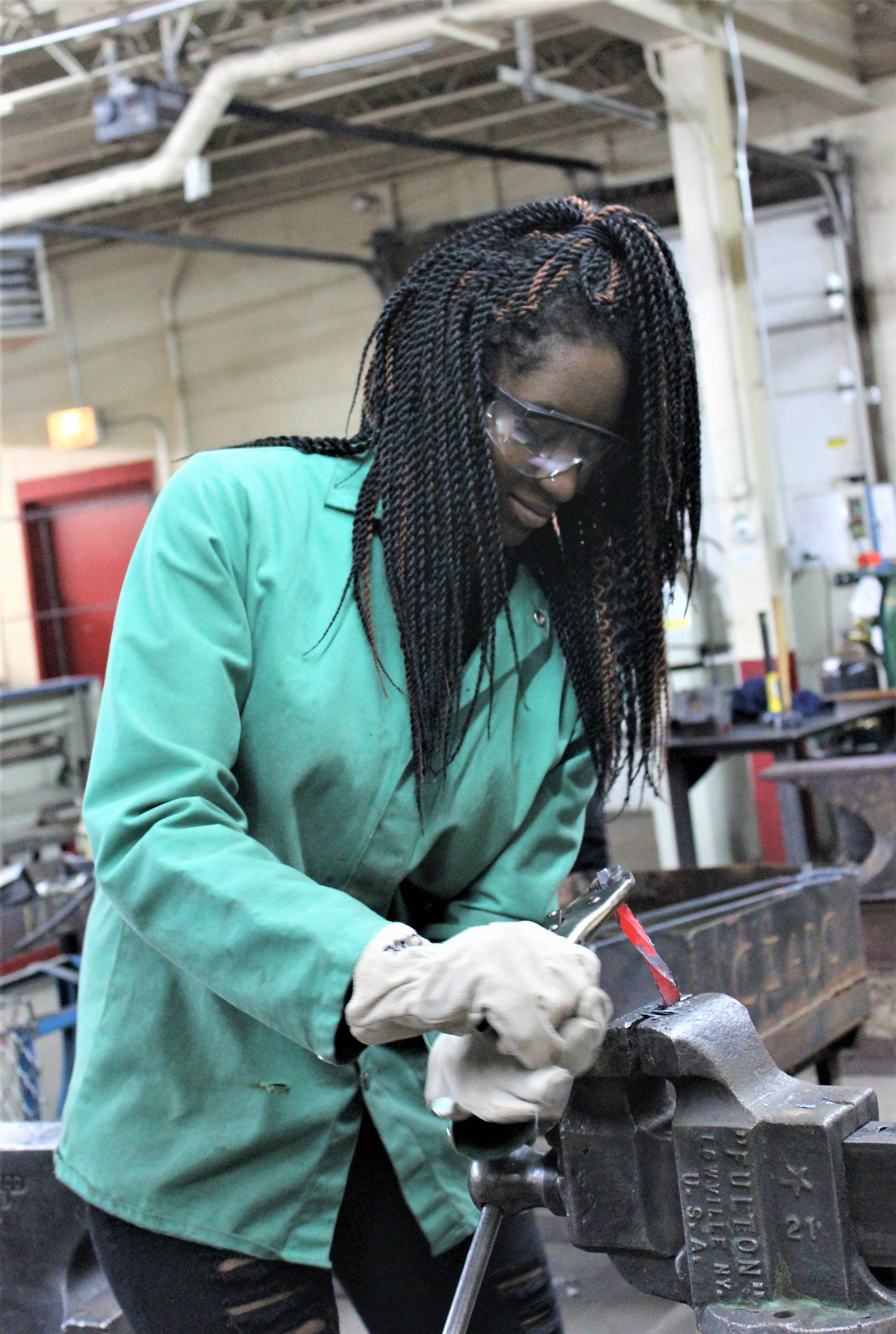

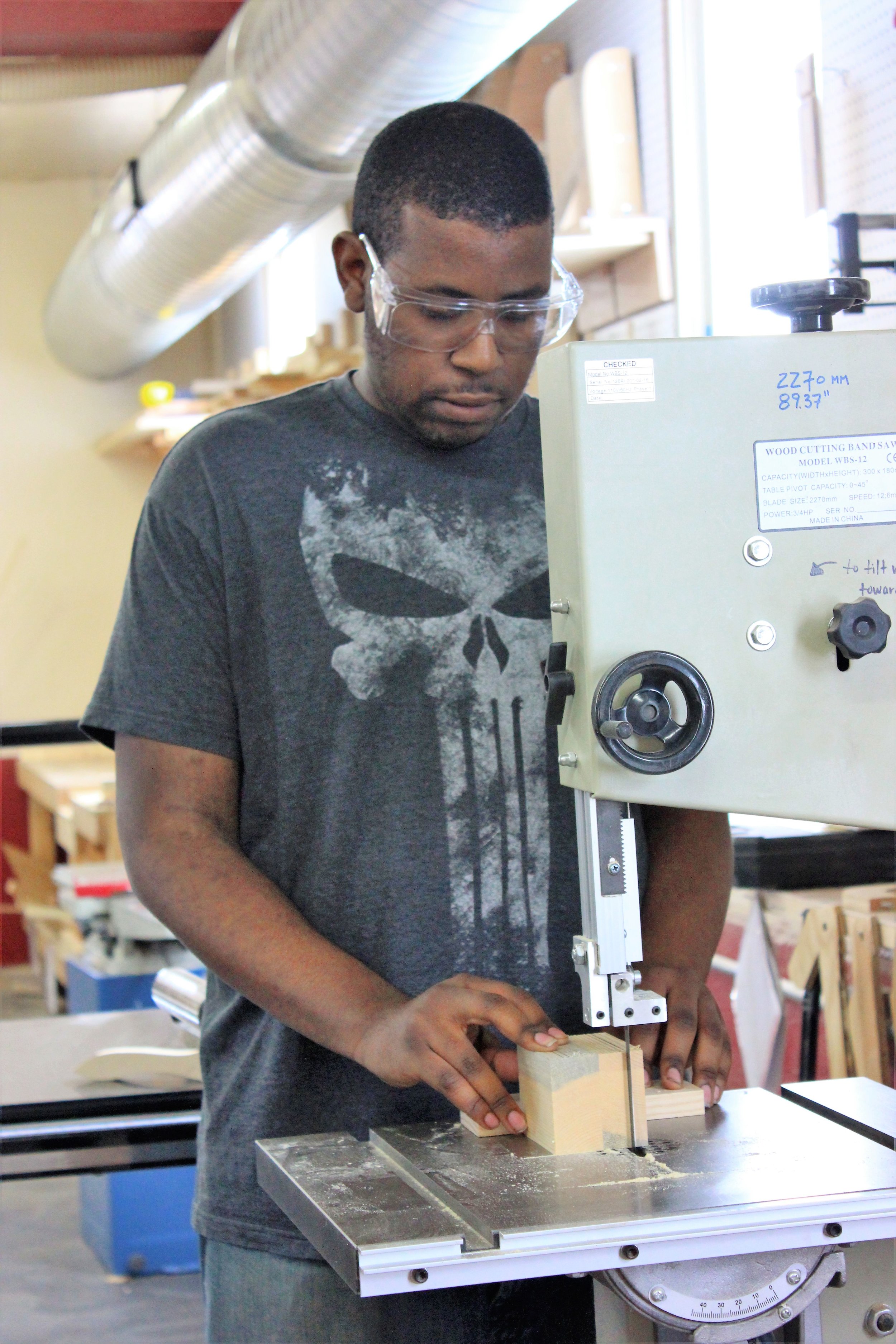

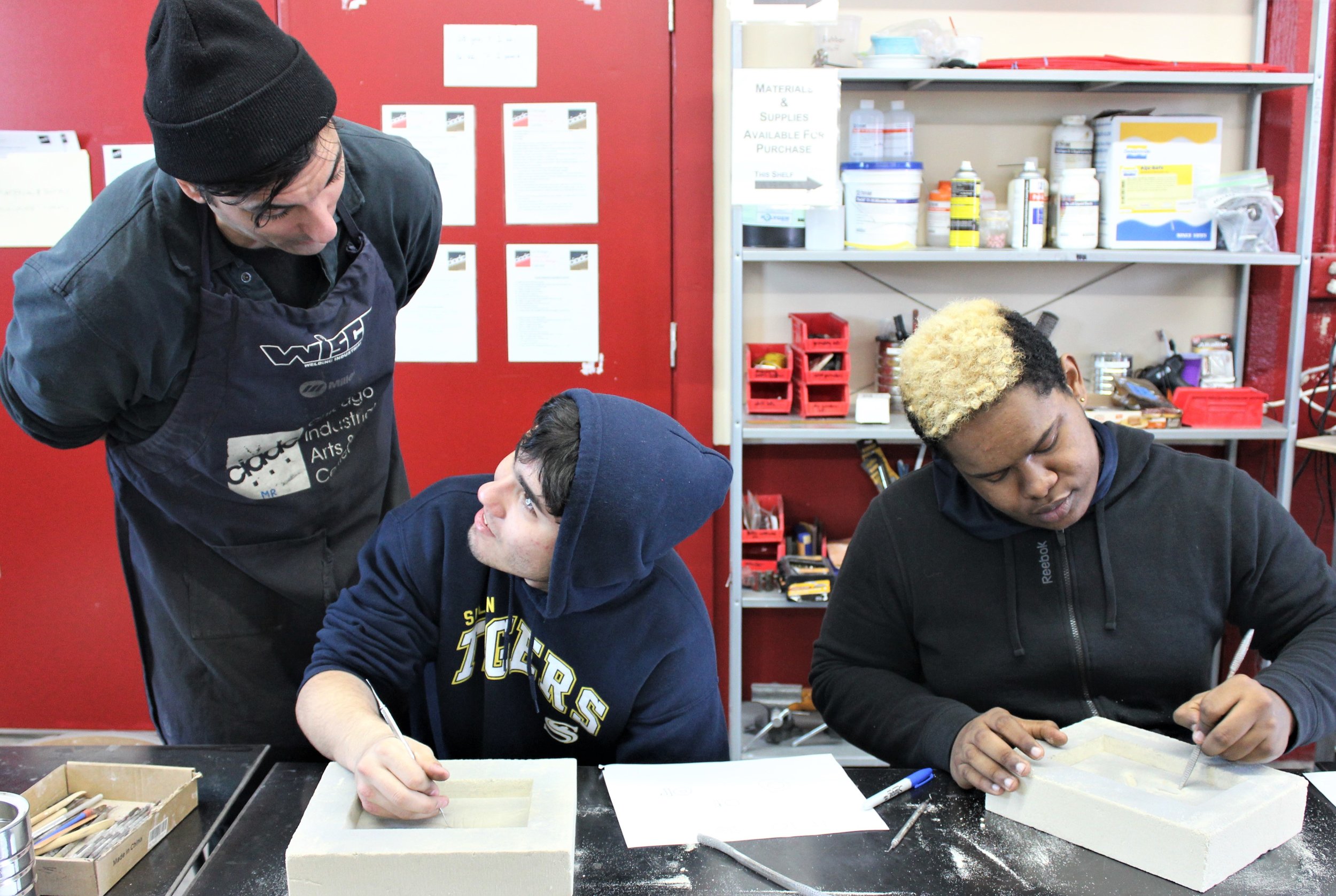
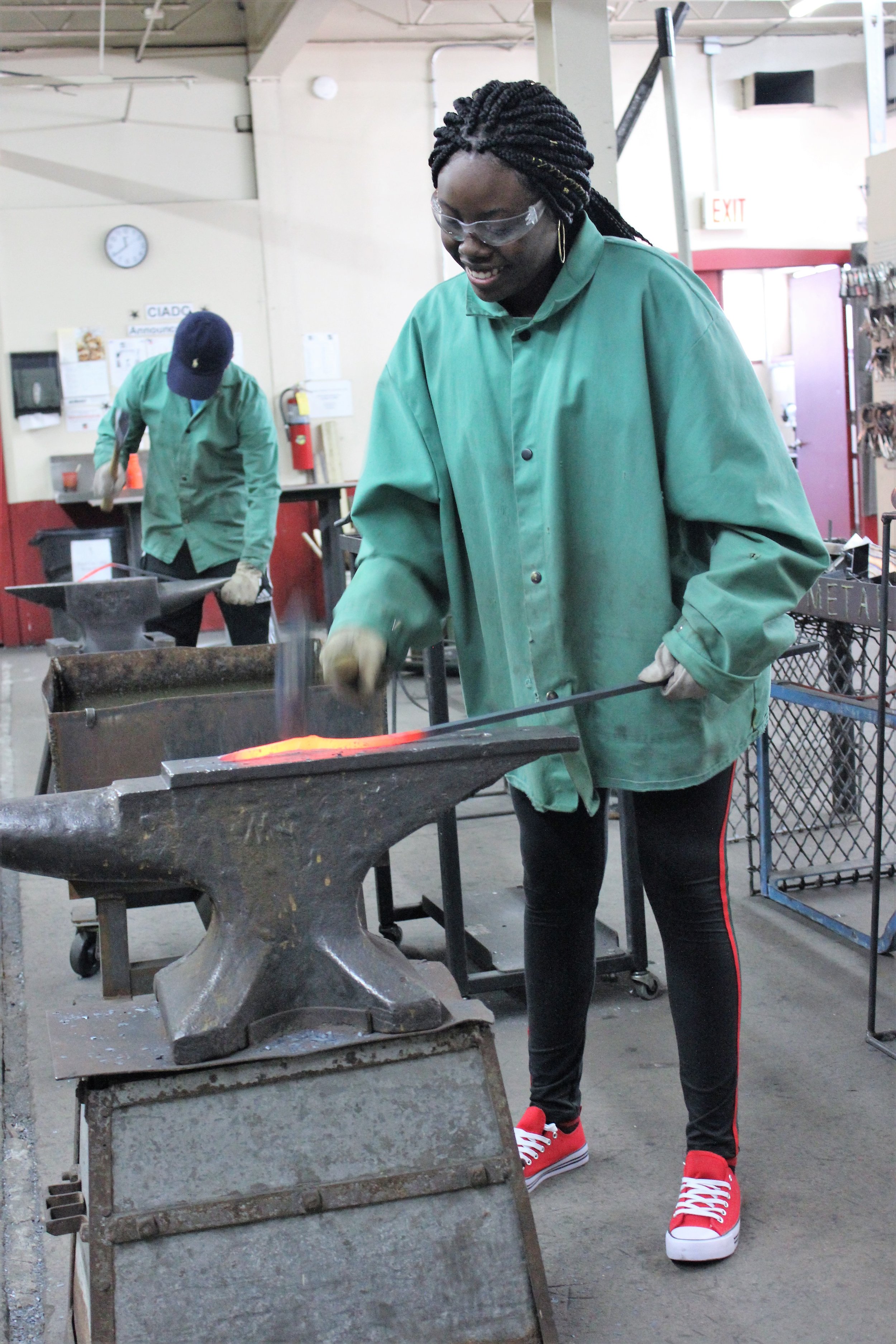
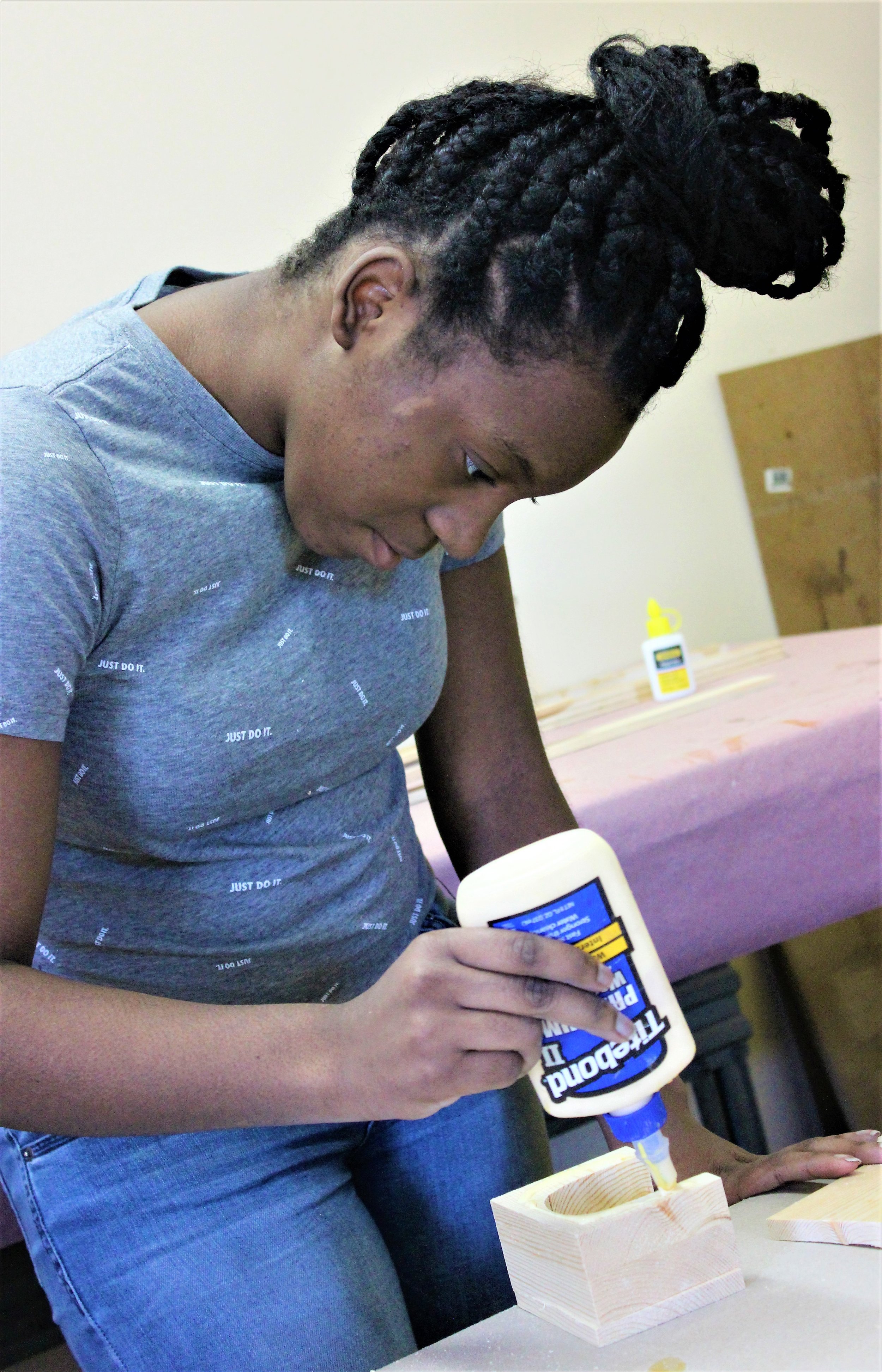
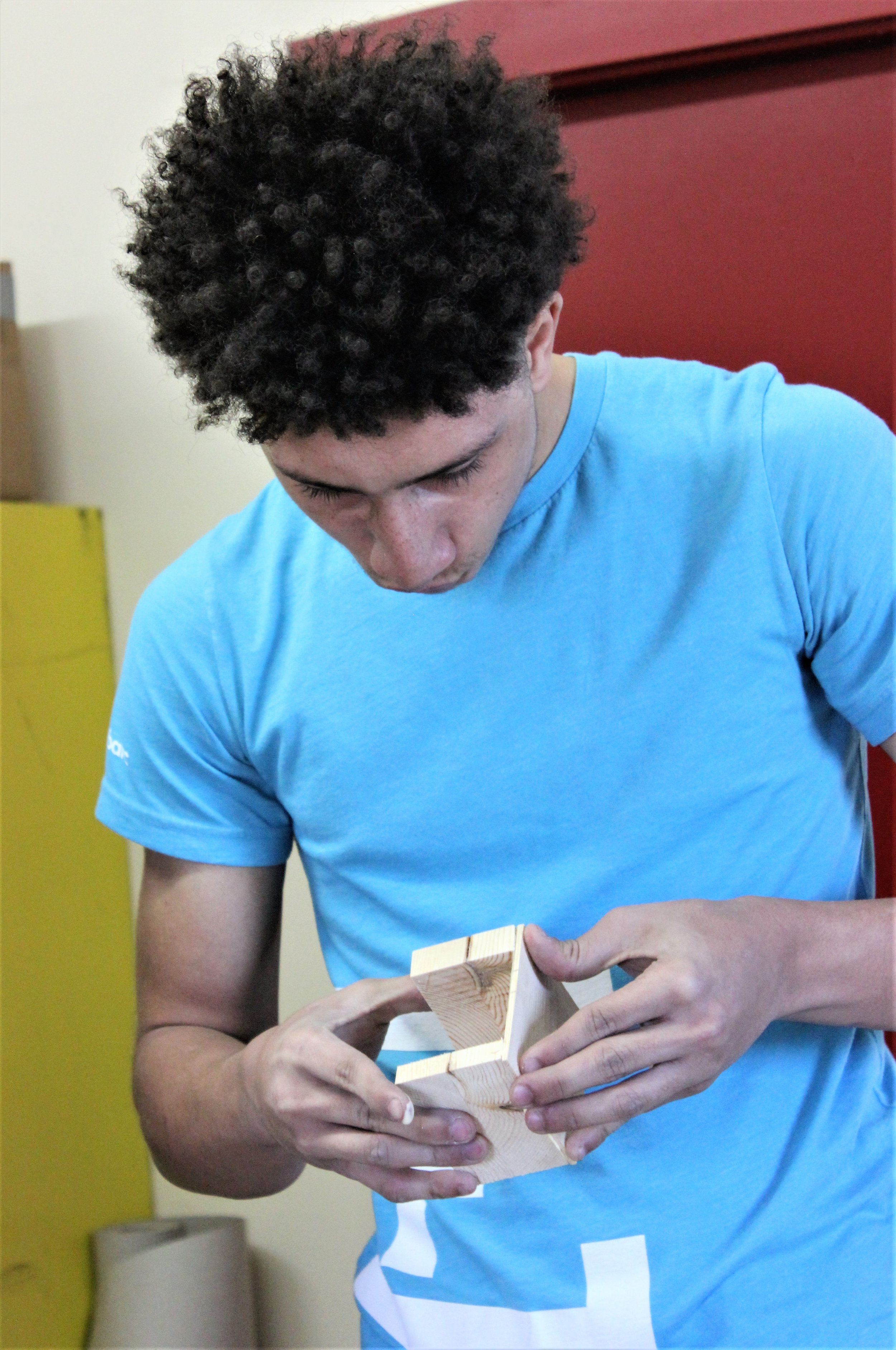
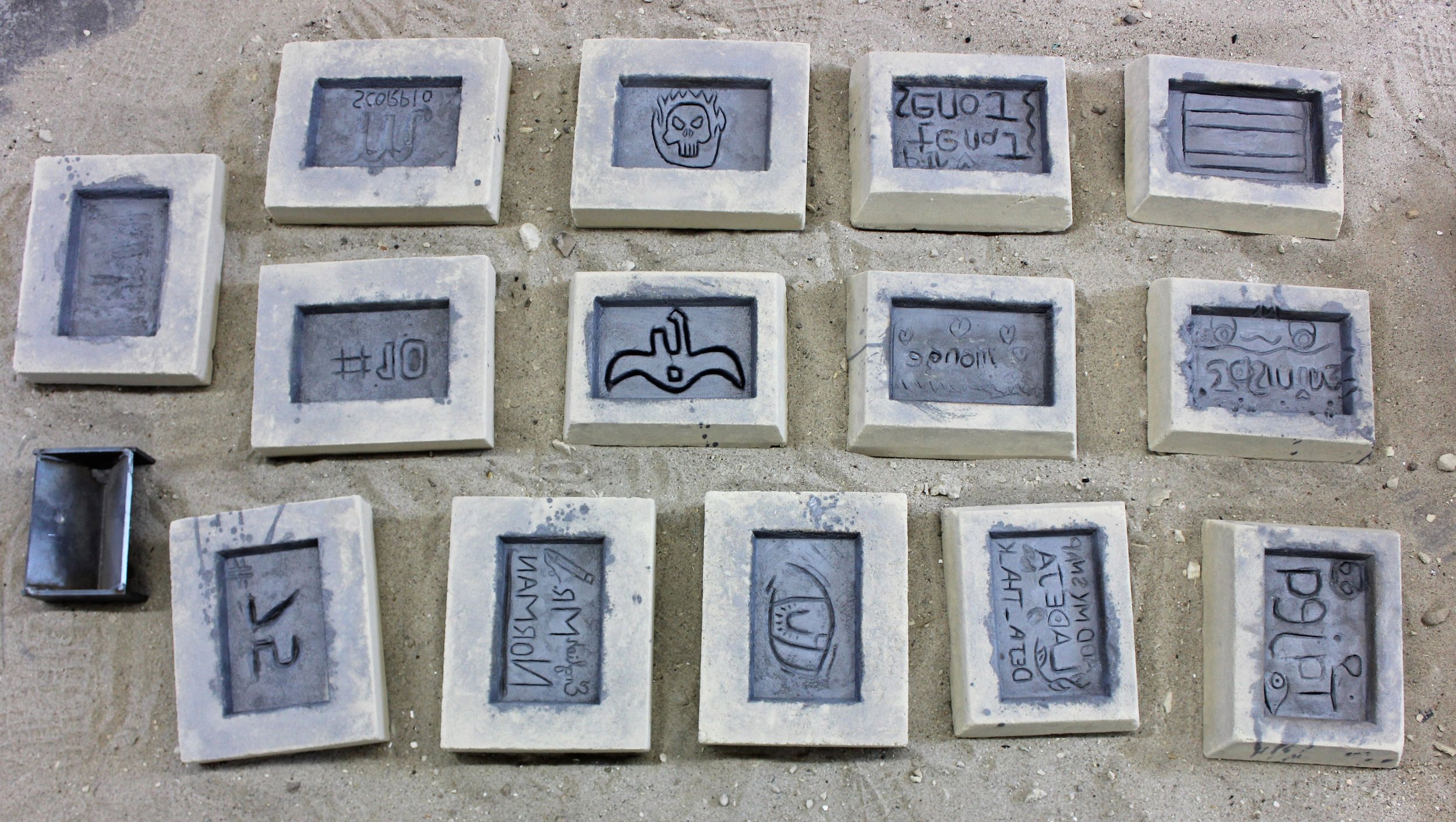
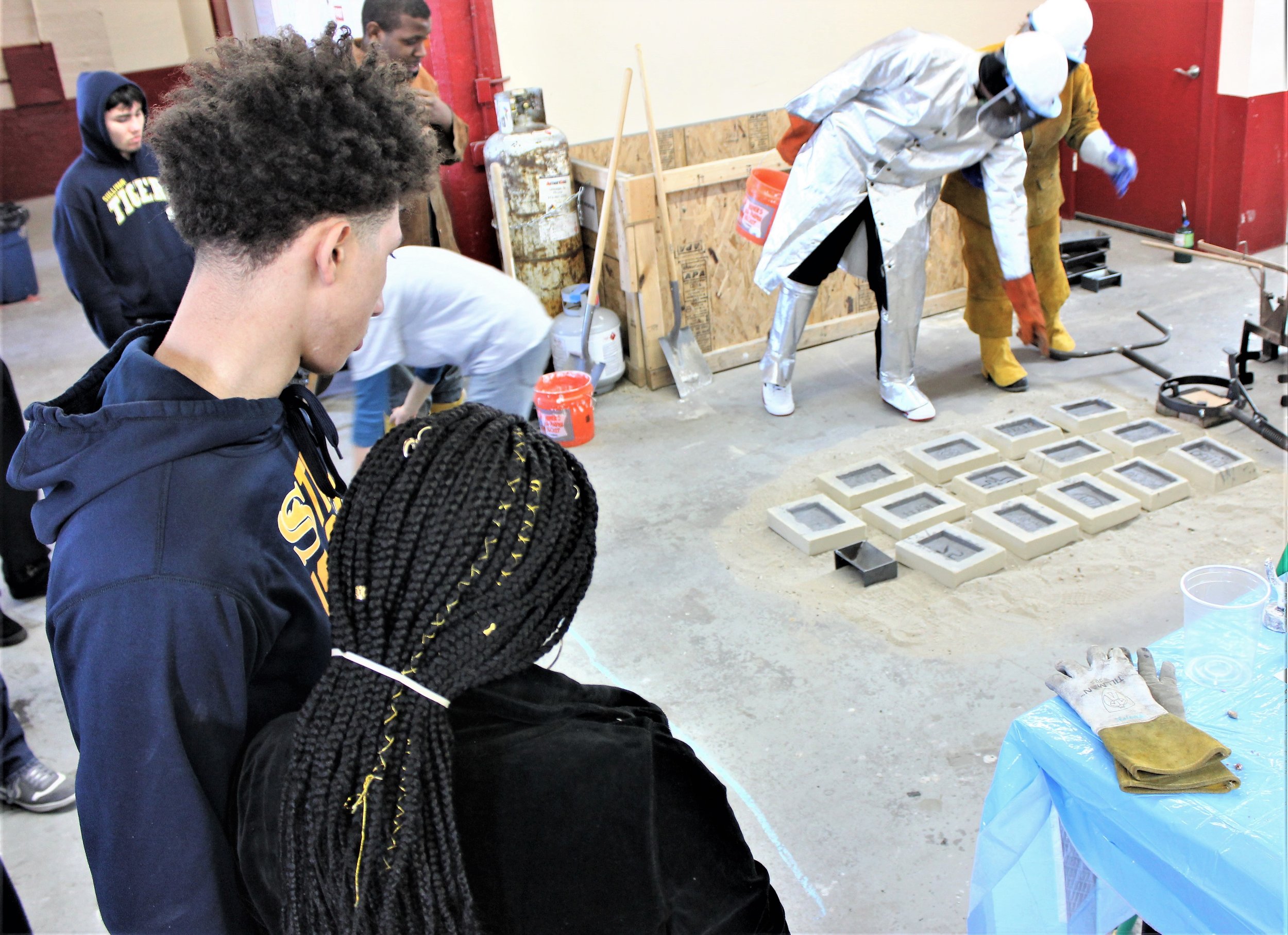
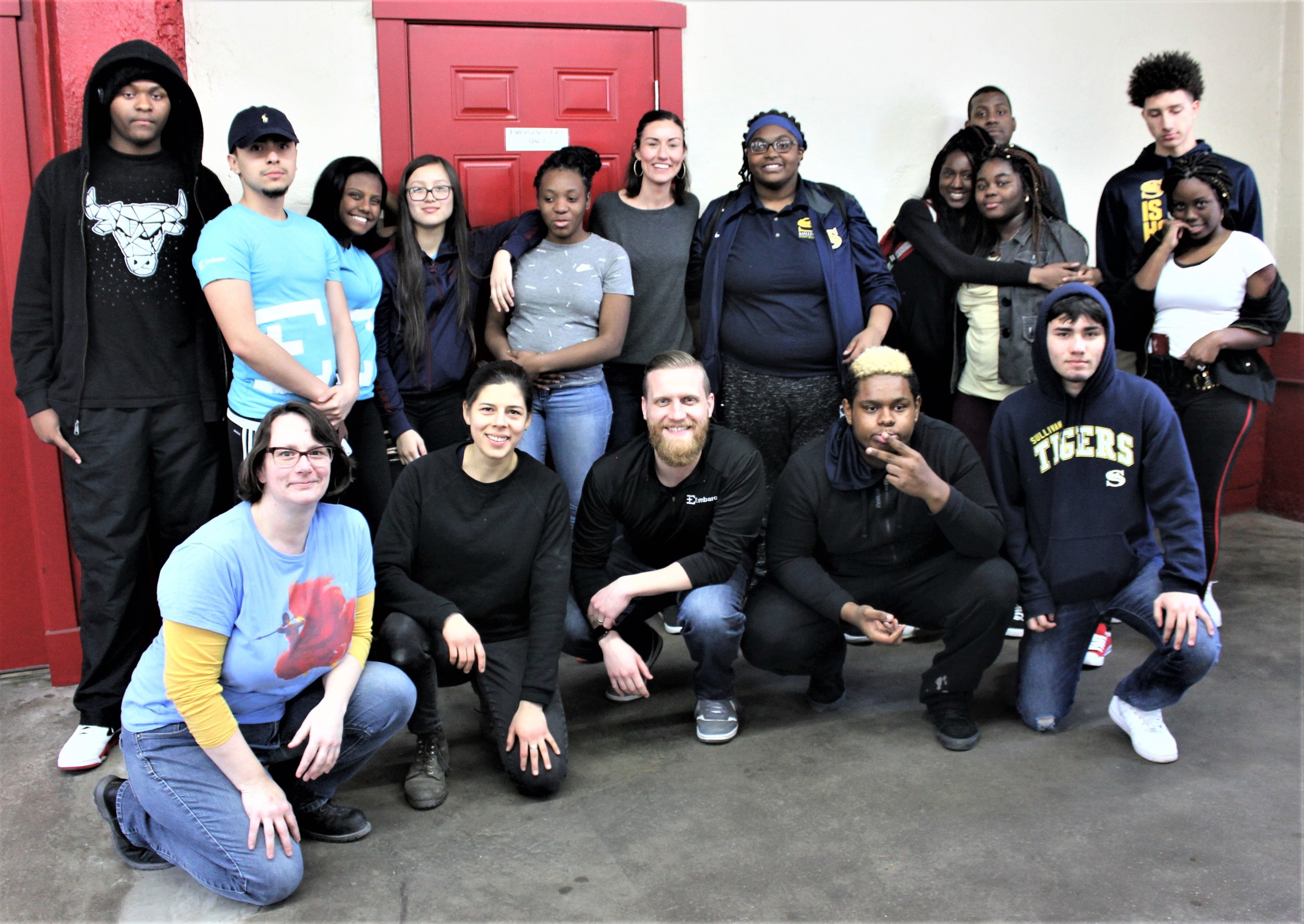
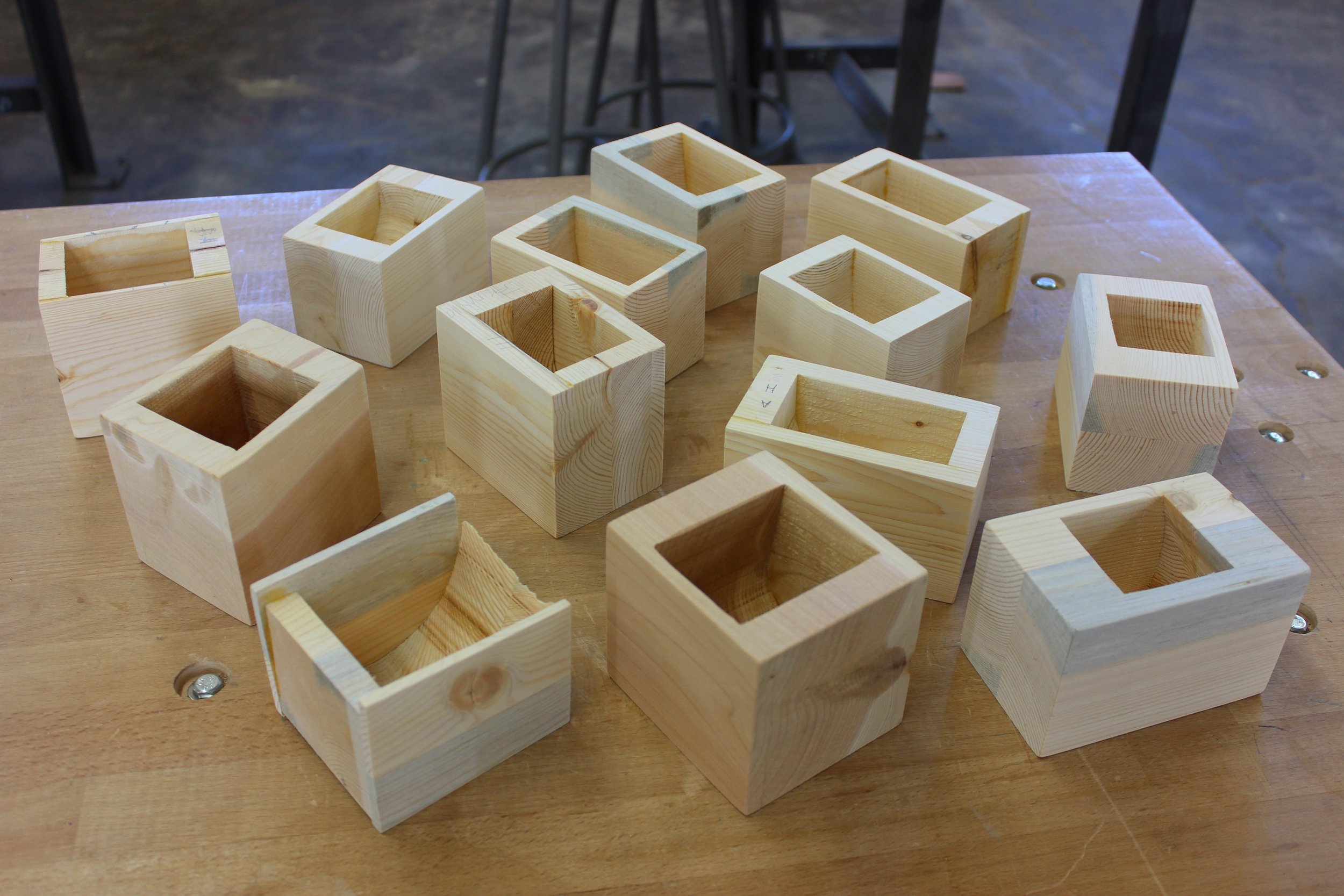
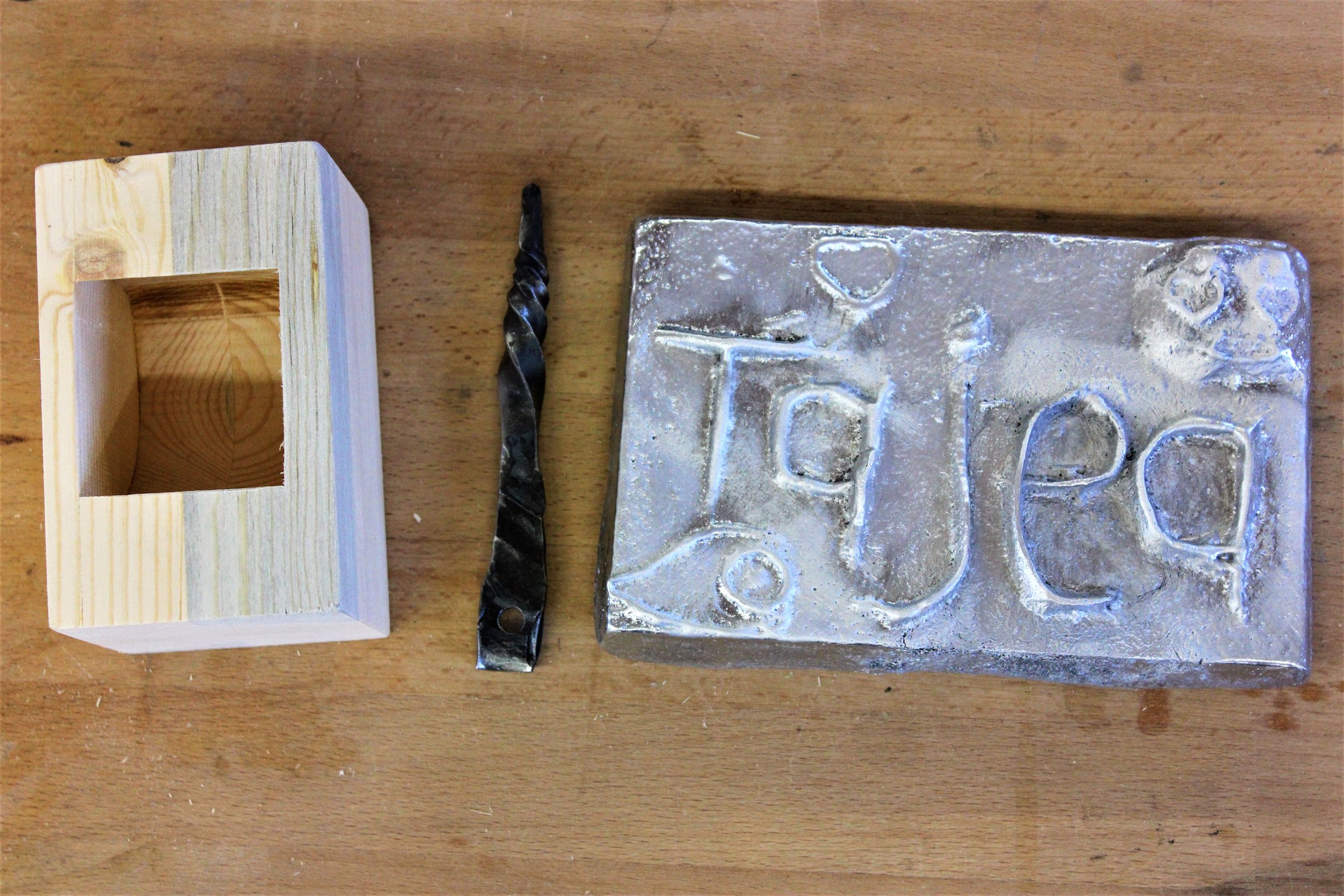
Embarc’s goal is to drive student success with long-term social and cultural exposure. Through the transformative power of these journeys, Embarc awaken students to the possibilities of their potential by dissolving the borders of the city and in their minds. Inspired by Embarc’s important work, CIADC is excited to announce the gift of 30 full-tuition scholarships to local teens. CIADC is working with both Sullivan High School and the Chicago Math & Science Academy to identify scholarship recipients.